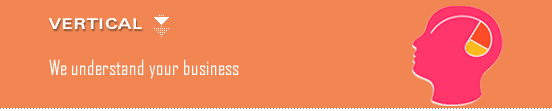 |
|
 |
 |
 |
As customer demands change, shifts in resource status and material availability can occur. Optimization Engine for Discrete Manufacturing enables companies to quickly react, synchronizing factory production plans and schedules to meet business challenges. It also assists buyers in performing efficient material planning by providing extensive modeling capabilities to solve a breadth of problems in the entire material planning process domain. The result is a plan tailored to meet customer delivery requirements and business objectives. |
 |
In addition to increasing profitability by reducing manufacturing lead-time, increasing delivery date performance, and reducing work-in-progress, Optimization Engine for Discrete Manufacturing can enable planners to: |
 |
 |
Immediately resolve potential problems in the supply chain |
 |
 |
Create optimal manufacturing plans against both finite and infinite capacity constraints |
 |
 |
Provide accurate due-date quoting to improve customer service |
 |
 |
Create powerful time-based report summaries |
 |
 |
Leverage Infynita Inc. experience to reduce both risk and time to value |
 |
|
Problem-oriented planning enables immediate resolution |
 |
Optimization Engine for Discrete Manufacturing's problem-oriented planning technique goes beyond simple constrained planning and exception-based reporting. Planners are provided with a list of potential problems based on demand on the system and constraints that exist. Planners can use the Problem Window to "drill down" into the details to investigate root causes of problems such as late orders, material shortages, or capacity shortages using "point-and-click" actions. Optimization Engine for Discrete Manufacturing's provides users with multiple tools to fix the problem such as expediting material, adding capacity by running additional shifts, or other available options. |
 |
Comprehensive support for both finite and infinite capacity planning |
 |
Current planning systems schedule operations based on either material or capacity constraints, but not both. What results is a never-ending adjustment of the plan to resolve various constraint issues because the planner considers material and capacity separately and assumes these resources are infinite. Optimization Engine for Discrete Manufacturing's finite capacity plans illustrate the ideal level of resource capacity needed to meet customer demand. Factory Planner flags overloaded resources, allowing the user to take corrective action in order to meet the delivery date. Users also have the choice of using Optimization Engine for Discrete Manufacturing's automated load balancing algorithms to create an optimal finite-capacity constrained plan automatically. |
 |
Accurate due-date quoting capability improves customer service |
 |
Optimization Engine for Discrete Manufacturing's memory-resident planning architecture provides the ability to model manufacturing problems involving complex bill of material structures, alternate part substitution, engineering changes, campaign constraints, multiple and re-entrant operations, and sequence-dependent set-ups. Factory Planner can also be integrated with order management systems, giving customer service representatives' capable-to-promise delivery date quoting or order status considering material and capacity constraints. |
 |
In addition, Optimization Engine for Discrete Manufacturing generates optimized production plans for a plant (or multiple plants), department, work cell, or production line by scheduling backwards from the requirement date, as well as scheduling forward from the current date, while simultaneously considering all key constraints. |
 |
Create powerful analytical reports |
 |
Optimization Engine for Discrete Manufacturing provides a wide variety of standard and user-customizable reports such as: |
 |
 |
Drill-down, hot links, and quick spreadsheet downloads |
 |
 |
User-defined columns, optional columns, filters, and summary groups |
 |
 |
Users are notified when newer data is available, allowing instant updates to match the latest plan. |
 |
 |
Highly customized time-based summary reports can be created with the easy-to-use, yet powerful Report Creation Wizard. |
 |
|
Leverage Infynita Inc.experience to reduce both risk and time to value |
 |
Production planning and scheduling are highly complex processes with specific needs for every vertical industry. Creating production plans requires knowledge of the business process as well as the industry-specific planning/scheduling knowledge of the problem. |
 |
The Optimization Engine suite of products has been built utilizing feedback garnered from planning experts and customers from many of the world's top manufacturers, then refined and improved through many successful implementations. Infynita Inc. has a deep understanding of the issues and key differences in the business planning problems of discrete manufacturers. |
 |
Partnering with Infynita Inc. reduces both implementation risk and time to value from the investment. |
 |
Key features |
 |
Fast, advanced planning and scheduling |
 |
 |
Heuristic planning and scheduling rules refined over years, with collaboration from planners of many of the world's top manufacturing companies using Optimization Engine |
 |
 |
Highly customizable for a wide range of industries and business objectives |
 |
 |
Highly scalable |
 |
 |
Extremely fast planning with world-class plan qualities - over 4,000,000 tasks planned in less than 10 minutes |
 |
 |
A powerful, fast memory-resident APS engine that generates plans in minutes as compared to hours in traditional MRP systems that use database-driven engines |
 |
 |
Capable-to-promise delivery date quoting, simultaneously considering material and capacity constraints |
|
 |
Modeling |
 |
 |
Multi level bill-of-material, alternate routings, routing segments, and routing attributes |
 |
 |
Alternate parts, use-up parts, phantom parts (kitting), attributed parts, subcontracted parts |
 |
 |
Purchase orders and procurements |
 |
 |
Variable yields, learning curves |
 |
 |
Simultaneous resources, pooled resources, aggregate resources, and parallel resources |
 |
 |
Resource calendars, supplier calendars, and receiving calendars |
 |
 |
Multiple suppliers, preferred suppliers, fair share across suppliers, and blanket purchase orders |
 |
 |
Lot-sizing (minimum, maximum, multiples, ideal) |
 |
 |
Batching (multiple strategies including hot lots, fixed, and variable runtimes) |
 |
 |
Sequence-dependent setups with multi-level setup rings |
 |
 |
Expediting |
 |
 |
Down binning with attribute distributions |
 |
 |
Prioritized demands, multi-line item demands, stock orders, forecast orders, and safety stock orders |
 |
 |
Finished WIP, unfinished WIP, pegged WIP, and un-pegged WIP |
 |
 |
Transfer batching, expiration dating, and lot tracking |
 |
 |
Setup time, minimum and estimated queue time, pre-op time, run time, cool down time, and transportation time |
 |
 |
Production cycles and block planning |
|
 |
|
|
|
|